MIXR
Magnetic Stir Bar - redesigned from scratch




-
The patent pending 'Daruma' (roly-poly) motion reduces vortex formation and enhances turbulence, greatly improving mass and heat transfer
-
The stir bar spins on a dynamic off-axis rotation (P) relative to the rotational axis of driver magnet (S)
-
-
Insights from CFD simulations have expanded the boundries of magnetic mixing
-
High-shear type: optimized for low viscosity, high RPM
-
High-turnover type: optimized for viscosity up to 1,500 cP
-
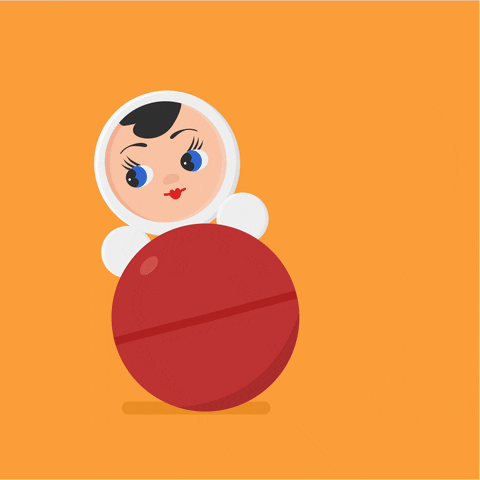
Our development approach combines CFD analysis with experimental validation to craft designs that deliver optimal mixing performance.


-
Vorticity: measures fluid rotation; higher vorticity leads to more vigorous mixing
-
Power number: a unitless factor of a design's efficiency in converting mechanical energy into fluid motion
-
Shear rate: how quickly layers of fluid move relative to each other
High-Turnover Design:
The SRS (Streamline Rotational Stirring) design generates 52X more power number than a conventional rod stir bar. This means it moves fluid more efficiently across the entire vessel, making it ideal for mixing thick liquids and speeding up circulation where it's needed most.
High-Shear Design:
The SDA (Shear Driven Action) design creates a shear rate that is 2.7X higher than conventional rod stir bar. This high shear rate helps break apart droplets and breaking up aggregates, and overcoming surface tension, improving the uniformity of the mix.
Selection Matrix

High-shear MIXR applications:
-
Emulsion
-
Suspension polymerization
-
Cosmetic creams
-
Ceramic slurries
-
Polishing compounds
-
Conductive inks
-
Nanoparticle suspensions
High-turnover MIXR applications:
-
Solid catalysts
-
Powder in resin, paints, and creams
-
Powdered flocculants
-
Polymerization reaction

Comparison Chart of Common Magnetic Stir Bar Types
Feature | FLXR Eng | Standard PTFE | PTFE Alternative |
---|---|---|---|
Outer Shell Material | PEN | PTFE | PEEK |
Association w/ PFAS | No | Yes | No |
Flow Character | Reduced-vortex | Vortex | Enhanced-vortex |
Viscosity Range | 1~1,500 cP | 1~500 cP | 1~1,170 cP |
Operating Temperature | -60~155 C | -100~225 C | -50~80 C |
Autoclave-able | Yes | Yes | Yes |
Gamma sterilization | Yes | No | Yes |
EtO sterilization | Yes | Yes | Yes |
Mix Hard Insoluable Particles | Yes | Not Recommended | Yes |
Est. Carbon Footprint | 3.4 kg CO2 eq/kg | 9.6 kg CO2 eq/kg | 7.6 kg CO2 eq/kg |
Magnet | SmCo | AlNiCo | NdFeB |
Flow Direction | Axial/Radial | Radial | Radial |
Usage Example
Sterilizing PEN Labware
Radiation resistance of PEN tested to be 10.6 MGy
